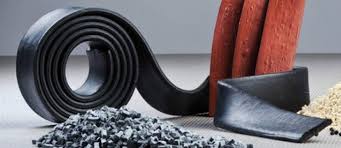
Rubber is one of the most versatile materials used in numerous industries, from automotive to healthcare and electronics. However, raw rubber cannot perform well in its natural state. It requires a specific process known as “curing” or “vulcanization” to enhance its properties such as durability, elasticity, and resistance to heat. This process is achieved using مواد پخت لاستیک, which are curing agents that initiate or accelerate the vulcanization reaction. In this article, we will explore the different types of curing agents used in rubber production, their functions, and how they contribute to creating high-performance rubber products.
What is Rubber Curing?
Rubber curing, or vulcanization, is a chemical process that involves cross-linking the polymer chains of rubber molecules through the use of heat and curing agents. This cross-linking improves the rubber’s mechanical properties, such as its strength, elasticity, and resistance to aging, oil, and other chemicals. The process of vulcanization changes the rubber from a soft and sticky substance to a durable, elastic material that can withstand different environmental conditions.
The curing process is essential in producing a wide range of rubber products, such as tires, seals, gaskets, hoses, and footwear. Curing agents, known as مواد پخت لاستیک, are critical in ensuring the final product meets the required specifications in terms of performance and durability.
Types of Rubber Curing Agents
There are several types of مواد پخت لاستیک used in the vulcanization process. The choice of curing agent depends on the type of rubber being processed, the desired properties of the final product, and the specific application. Here are some of the most commonly used curing agents:
1. Sulfur-based Curing Agents
Sulfur is the most traditional and widely used curing agent for rubber. The process of sulfur vulcanization is responsible for creating a network of cross-links between the rubber molecules. This network structure enhances the rubber’s elasticity, strength, and resistance to aging.
The sulfur vulcanization process usually involves adding sulfur to the rubber compound in the presence of heat. The sulfur atoms form bridges between the polymer chains, creating a three-dimensional network. The amount of sulfur used and the curing temperature determines the properties of the rubber. The higher the sulfur content, the stronger and more heat-resistant the rubber becomes.
2. Peroxide-based Curing Agents
Peroxide-based curing agents are an alternative to sulfur-based systems. These agents work by decomposing at high temperatures to produce free radicals, which initiate the cross-linking of the rubber molecules. Peroxide vulcanization offers several advantages, such as improved heat and weather resistance, low compression set, and better electrical insulation properties.
Peroxide curing systems are particularly useful for certain types of rubber compounds, such as those used in automotive and electrical applications. The use of peroxides is also preferred in some cases where sulfur vulcanization may lead to undesirable side effects, such as the formation of sulfur bloom (a powdery residue that forms on the surface of the rubber).
3. Resin-based Curing Agents
Resin-based curing agents are used to improve the processability and performance of rubber compounds. These curing agents typically consist of resins that interact with the rubber matrix, leading to improved cross-linking. They are often used in combination with other curing agents, such as sulfur or peroxides, to enhance the overall curing process.
Resin curing agents are particularly useful in the production of rubber materials that require specific surface properties or enhanced adhesion to substrates. For example, in the automotive industry, resin-based curing agents can be used to improve the bonding between rubber and metal components.
4. Metal Oxides
Certain metal oxides, such as zinc oxide and magnesium oxide, are also used as curing agents in rubber production. These oxides act as activators in sulfur vulcanization systems, enhancing the effectiveness of sulfur and promoting the formation of cross-links. Zinc oxide, in particular, is commonly used in the production of rubber tires and other high-performance rubber products.
While metal oxides do not directly contribute to the cross-linking process, they play a vital role in the vulcanization process by facilitating the chemical reactions that lead to the formation of cross-links. They also improve the aging resistance and overall durability of the rubber.
The Role of مواد پخت لاستیک in Rubber Properties
The choice of curing agent, or مواد پخت لاستیک, significantly influences the final properties of the rubber product. Here are some of the key attributes that curing agents affect:
1. Elasticity
One of the most important properties of rubber is its elasticity – the ability to return to its original shape after being stretched or compressed. Curing agents, particularly sulfur-based agents, create cross-links that enable rubber to regain its shape quickly and effectively. This property is crucial for products such as tires, seals, and gaskets, which must maintain their functionality even under stress.
2. Durability
Durability refers to the ability of rubber to withstand wear and tear over time. Curing agents play a crucial role in enhancing the rubber’s resistance to environmental factors such as heat, UV light, ozone, and chemicals. By forming a network of cross-links, curing agents increase the strength and toughness of the rubber, making it more resistant to degradation and extending its lifespan.
3. Resistance to Heat and Chemicals
Many rubber products are exposed to harsh conditions, including high temperatures and aggressive chemicals. The use of specific curing agents, such as peroxides or metal oxides, can improve the rubber’s heat resistance and make it more durable in chemical environments. For instance, peroxide-based curing systems can enhance the thermal stability of rubber compounds, making them ideal for high-temperature applications.
4. Flexibility and Processability
In addition to improving strength and durability, curing agents also influence the flexibility and processability of rubber. Certain curing systems allow for better processing of the rubber, making it easier to mold and shape into the desired form. For example, resin-based curing agents can improve the surface properties and ease of molding, which is essential in the production of intricate rubber components.
The Future of Rubber Curing Agents
As technology advances, there is a growing demand for more efficient and environmentally friendly curing agents. Researchers are exploring new materials and methods for vulcanization that reduce the environmental impact of rubber production. For example, the use of bio-based curing agents and the development of low-emission curing systems are areas of active research.
In addition, there is a push toward improving the performance of rubber products by using advanced curing agents. With the increasing demand for high-performance materials in industries such as automotive, aerospace, and electronics, the role of مواد پخت لاستیک in shaping the future of rubber technology cannot be overstated.
Conclusion
مواد پخت لاستیک, or rubber curing agents, are essential components in the vulcanization process that transforms raw rubber into a durable, elastic, and heat-resistant material. Whether it’s sulfur-based curing agents, peroxide systems, or resin-based solutions, the choice of curing agent plays a significant role in determining the performance and longevity of rubber products. As the rubber industry continues to evolve, the development of more efficient and sustainable curing agents will be key to meeting the growing demands of various sectors.